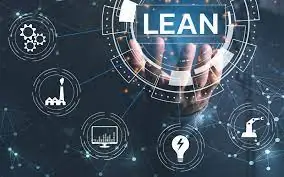
What is a Lean Supply Chain?
Explore the world of Lean Supply Chain – a strategic approach inspired by Toyota's principles. Learn how to reduce waste, optimize efficiency, and boost collaboration. Discover real-life case studies, tools like VSM and Kanban, and the impact of technology. Enhance your supply chain with ERP, WMS, and automation. Overcome common challenges and build a more efficient, responsive, competitive supply chain.
What is a Lean Supply Chain?
A lean supply chain is both a philosophical concept and a business strategy. The lean supply chain strategy aims to reduce waste while optimizing efficiency during goods and services production and distribution processes. The term is derived from the “lean manufacturing principles” developed by Toyota for their Toyota Production System.
Implementing a lean supply chain will be a continuous journey requiring a company culture shift. All team members must be committed to converting to a lean supply chain for it to work. And while the supply chain adaptations will surely take effort, the resulting optimization will be well worth the switch! Common benefits of adopting lean principles include reduced costs, improved quality, faster leads, and increased customer satisfaction.
Table of Contents:
- What is a lean supply chain?
- Core Principles and Fundamentals
- Real-Life Examples
- Tools and Techniques
- VSM Mapping
- Kanban Method
- Six Sigma
- Collaborative Relationships
- Reducing Lead Times
- Supplier Integration
- Real-world Case Study
- Emerging Technology
- ERP
- WMS
- Automation and Robotics
- Common Challenges
- Strategies and Solutions
- Risks and Pitfalls
- Conclusion
We provide competitive freight shipping prices and an all-inclusive, easy-to-use shipping experience for our customers. Exceeding our customers’ expectations results in thousands of satisfied customer reviews and repeat business. We believe in the power of our customer relationships. Check out FreightCenter reviews from real customers, and learn what they have to say about their freight shipping experience!
Awards and Endorsements
- 2021 Food Logistics’ Top Green Providers
- 2021, 2017 & 2016 Food Logistics’ Top Green Providers
- 2021 & 2018 Supply & Demand Chain Executives’ Pros to Know: Matthew Brosious
- 2020 & 2019 Top Food Logistics’ 3PL & Cold Storage Provider Award
- 2020 & 2019 Business Observer’s Top 500 Companies on the Gulf Coast
- 2020 & 2017 SmartWay® Transport Partner
- 2020 & 2017 Food Logistics’ Champions: Rock Stars of the Supply Chain
- 2020 Best of Palm Harbor Awards for Local Businesses
- 2017 Green Supply Chain Award from Supply & Demand Chain Executive
- 2017 Tampa Bay Business Journal Heroes at Work
- 2016, 2015, & 2012 Food Logistics Top 100 Software and Technology Providers
- 2013 Top 100 Great Supply Chain Partners by SupplyChainBrain
- 2012 TIA Samaritan Award Honorable Mention
- 2012, 2011 & 2010 TBBJ Fast 50 Recipient
- 2013, 2011, & 2010 Diversity Business Top Businesses
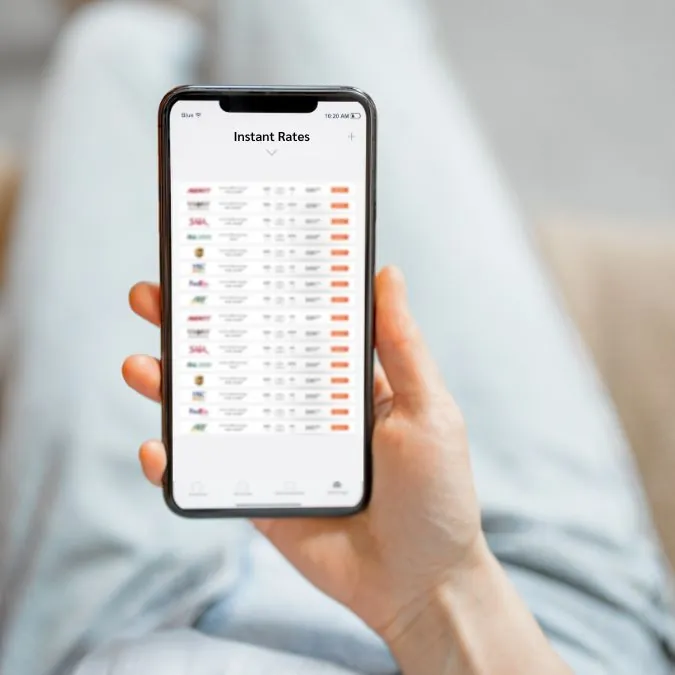
Why Opt For Our Freight Quotes?
- Shipping Quotes anytime
- Access shipping quotes anytime for destinations across the U.S. & Canada.
- Enjoy unmatched discounts on LTL, truckload, rail, air, and more.
- Benefit from automated freight tracking, paperwork, and invoices.
- Simplify management by keeping all quotes and shipments in one place.
- Leverage over 24 years of logistics expertise working for you!
Choosing Your Carrier
Opting for a 3PL like FreightCenter can lead to significant cost savings. When you entrust your shipping to FreightCenter, you’ll enjoy exceptional service at a fraction of the price. The secret? Competition. FreightCenter is the platform where top carriers vie for your business. Need evidence?
Use our instant freight quote tool to receive estimates from numerous carriers, or speak to one of our freight shipping experts by calling us at 800.716.7608.
Core Principles and Fundamentals
At the core of the Lean Supply Chain approach is the strategic focus on minimizing waste and creating an optimally efficient environment. Ideal leads, time frames, and quality do not just appear out of thin air. If your company wants to develop a lean supply chain, you must focus on integrating the following Lean Supply Chain principles.
Just-in-Time Inventory Management (JIT): The JIT concept represents demand-driven production, meaning products and services are produced in response to customer demand, as opposed to the forecasting method. Manufacturing that responds to customer demand helps to prevent overproduction, as well as excessive inventory. Another result of this approach is the reduced inventory levels, which also work to reduce carrying costs, storage space requirements, and obsolescence risk. JIT requires close collaboration with suppliers to ensure timely delivery and meet customer demands with minimal delays.
Continuous Improvement (Kaizen Culture): Kaizen is a culture of continuous improvement, a concept ingrained in the lean supply chain. Essentially, Kaizen is an attitude all team members embrace that encourages regular, small improvements in the supply chain process in everything from systems to products. The philosophy encourages employees to participate actively in the improvement process, which presents an insider take and creates a sense of empowerment among workers.
The focus of “Kaizen” is to identify and eliminate differing types of waste, including overproduction, excess inventory, defects, and avoidable processing. Like all other lean supply chain principles, Kaizen is a process of continual refinement, best improved by regular assessments and reviews.
Lead Time Reduction: Streamlining supply chain processes is one of the most effective ways to eliminate delays and inefficiencies further. The elimination of delays results in reduced lead times. This trickle-down effect allows companies to respond more quickly and effectively to customer demand. Shorter leads create supply chain agility, crucial in today’s modern business environment, where market conditions change constantly.
Improved Quality: While other supply chain approaches may rely on inspection and correction, lean supply chains focus on implementing quality processes. As a result, this approach reduces the probability of defects and ensures high-quality products and services. Another aspect of continuous improvement is feedback loops. Feedback loops allow workers to identify and address issues concerning quality with a sense of urgency. Consequently, processes are continually refined, and product quality is improved.
Increased Profitability: Increased profitability is another fundamental principle of a lean supply chain, accomplished through cost reduction and customer satisfaction. Lowering operating costs by reducing waste and inventory will positively impact profitability. Likewise, delivering high-quality products within an efficient time frame will improve repeat customer rates.
To create value for our customers by delivering customized shipping solutions that meet their unique needs and to fulfill shipping demands from simple to complex with expertise, guidance and ingenuity.
Rely on the professionals at FreightCenter for competitive rates and a wide range of choices to meet your LTL freight shipping requirements.
We provide tailored solutions for both full and partial truckloads, offering competitive pricing for dry van, flatbed, and refrigerated freight. Trust us to meet all your full truckload shipping requirements.
Our Nationwide Expedited Trucking services ensure the secure and swift movement of your freight. Whether it's a single large box or a full truckload, our freight shipping experts are equipped to deliver your shipment quickly.
Access the most dependable rates for Specialized Freight Services from leading carriers with just a few simple steps. Whether you need white glove service or international shipping, we have your needs covered.
Utilize flatbed trucks to accommodate and transport oversized or uniquely shaped shipments with ease and efficiency. These specialized vehicles offer the versatility needed to securely and safely transport cargo that exceeds standard dimensions or has unconventional shapes.
Optimize your shipping strategy by integrating various transportation modes, including trucking and rail, to enhance efficiency and achieve cost-effectiveness.
Utilize rail transport for extended distances or when handling multiple packages during the shipping process.
Transport goods in containers aboard cargo ships for international shipping.
Opt for air transportation when time-sensitive delivery shipments is required.
Arrange for trucking services to transport packages across international borders.
Engage specialized heavy haul trucking services for oversized or cumbersome shipments.
A third-party logistics provider is a company that offers enhanced and cost-efficient supply chain and logistics solutions to other businesses.

Collaborative Relationships
Collaborative relationships are essential to a lean supply chain. Developing collaborative relationships with suppliers involves coordinating with suppliers, customers, and other partners to optimize the overall process. Collaborating with suppliers involves joint planning, forecasting, production planning, and inventory management. Building a collaborative relationship also requires transparency in sharing information, such as production schedules and demand forecasts, and aligning both sides with the lean supply chain model.
Customers are another essential collaborative relationship. It is necessary to understand customer demands, preferences, and requirements. Companies can and should utilize feedback loops to understand their customers better. Attaining feedback on product quality, delivery times, and general satisfaction is crucial to making proper adjustments and improvements.
Integrating information technology is a no-brainer when establishing collaborative relationships with suppliers. Integration allows for real-time data sharing, making the entire process seamless. This improves visibility and coordination throughout the supply chain! EDI (Electronic Data Interchange) is another tech tool you should use. EDI allows for the electronic exchange of business documents like purchase orders and invoices, streamlining all the manual processes usually involved.
Additional components of successful collaborative relationships include risk management, flexible agreements, and common ground in performance goals and metrics. Like any relationship, collaborative relationships with suppliers are a two-way street; partners must take responsibility for their actions, at least in any successful relationship. Lean supply chain partners must work together to mitigate risks and solve problems.
It all boils down to clear and open communication (promptly), coordinating resources, and working together to find solutions as they arise. If your company already implements Kaizen principles, this collaboration strategy will likely be easy for you, which inevitably encourages suppliers and customers to identify and implement improvements. The approach also promotes shared responsibility for continuous improvement and refinement of processes.
Effective communication also often lends itself to more flexible contracts and agreements. Flexible agreements and contracts allow partners to adapt to changing market demand, fluctuations, and other uncertainties as they arise. Long-term partnerships are also a massive boost to collaboration efforts; the longer supply chain partners have worked together, the more likely they are to trust each other, have a deeper understanding of each other, and work together more effectively.
Having shared goals and performance metrics will unify your vision and partnership. The goals of all supply chain partners need to be aligned for mutual success. A critical part of developing shared goals is through sharing performance metrics. This helps ensure all parties work towards the same benchmarks, enhancing supply chain efficiency. Sharing and setting goals and metrics indicates quality communication and trust, the cornerstone of successful collaboration.
You can expect a more responsive and efficient supply chain if your company prioritizes establishing clear communication channels and trust. Be aware that these relationships require ongoing effort and are dynamic, keeping you on your toes. Putting in the work to establish clear communication will help your company address issues faster and make timely decisions. Collaborative efforts benefit both companies. Trust makes it much easier for partners to rely on each other, share sensitive information, and work together to achieve a shared vision.
Reducing Lead Times
In a sense, collaborative supplier relationships help reduce lead times because they are collaborative. These relationships allow for greater visibility into demand patterns, which enables them to adjust to the forecasts, thereby reducing lead times. Previous efforts to optimize production schedules and implement lean manufacturing principles ensure goods and services are produced at the right time in the right amount, which minimizes delays and setbacks and reduces waste.
Collaborative forecasting fostered by collaborative relationships is an effective way to reduce lead times because suppliers can effectively plan production schedules and reduce the risk of stockouts or overproduction. Creating supply chain agility (fostered by supplier integration) is another way to reduce lead times. An agile supply chain can adapt quickly to changes in demand, order quantities, specs, and delivery schedules. Another way lead times are reduced is through risk mitigation. When companies work closely with their suppliers, they can more quickly identify and address risks, decreasing lead times.
Supplier integration and collaboration are crucial to reducing lead times. Open communication, shared information, and an aligned vision help create a more efficient and responsive supply chain.
Supplier Integration
What is supplier integration? Supplier integration is a supply chain management approach emphasizing collaboration between companies and suppliers. The goal is to create a seamless flow of materials, information, and processes. Integration requires joint planning and aligning production schedules, timelines, and product quantities. Companies and suppliers collaborate in forecasting to understand demand, share information, coordinate inventory management, and collaborate on product development. When supplier integration is done correctly, lead times and inventory levels can be significantly reduced, maintaining a smooth and efficient lean supply chain.
Real-World Case Study
Do not just take our word for it! Collaborative supply chain relationships have a lot of potential for business success. Dell Computers is just one example of the success that can occur when companies build quality collaborative relationships within their supply chain. For example 1995, Dell Computers developed the “Dell Direct Model”.
To accomplish this, the company reduced its supplier companies from 204 to 47. Then the remaining suppliers began warehousing their components just fifteen minutes from the Dell Factory to accomplish the JIT (just-in-time) inventory system. The JIT approach decreased inventory costs, enhanced customization, and customer satisfaction, and led to a 6% profit advantage for components that benefitted the consumer. Products were completed and ready for shipment within thirty-six hours using this approach.
Integrated supplier and distributor networks were crucial to Dell Computer’s success. Inventory turnover time was reduced by 57%, and production space was expanded. Dell’s collaborative relationships with suppliers made their 50% growth rate for three years possible and their $12 billion annual sales by 1997.
Emerging Technology
Advanced technologies such as Blockchain and IoT enhance lean supply chain management by boosting transparency, efficiency, and traceability. Blockchain technology acts as a ledger that records all transactions across a supply chain, allowing stakeholders to see this critical data in real-time. Since Blockchain is decentralized, it also will enable stakeholders to trace the origins and journey of products because information cannot be altered once recorded.
Blockchain makes the headache of product recalls and complying with regulatory requirements a breeze with a clear information trail that cannot be changed once recorded! This transparency creates better demand forecasting and improves inventory management. As a result, lead times are reduced, and excess inventory is minimized.
Blockchain makes automation possible for various tasks, reducing the risk of errors and helping to streamline the supply chain. The technology also fosters trust within the supply chain because information is transparent, secure, and cannot be tampered with, making collaboration stress-free!
The IoT (Internet of Things) is another essential supply chain management technology. This technology can churn out vast amounts of data through continuously monitoring the supply chain sectors, including warehouses, production lines, and transportation. With real-time insights, the IoT also contributes to a more responsive supply chain due to the real-time insights. IoT even contains sensors and RFID tags that allow for precise tracking of goods, monitoring conditions like temperature, humidity, and product location, and even providing info on how the product is being stored and transported, boosting product quality and safety.
Sensors on the manufacturing equipment can reorder raw materials when inventory is low, speeding up decision-making. As you can see, the IoT has a very accurate eye on the inner workings of the supply chain, allowing mistakes and defects to be quickly caught and corrected. Predictive maintenance helps reduce downtime, optimize equipment, and trim down waste. One of the most significant benefits of IoT is its inherent collaboration and trust-promoting qualities.
Blockchain and the IoT are emerging technologies that boost lean supply chain capabilities. Integrating the technology can help to create a smoother flowing and leaner supply chain.
ERP
Enterprise resource planning systems (ERP) help support lean supply chains in various ways, from centralized information management to integrated processes and cost control. ERP provides a centralized data platform to manage and store business information, inventory levels, order status, and production schedules.
It supports the lean approach because stakeholders have access to critical information. ERP also integrates business processes such as procurement, production, and order fulfillment, allowing for an effortless flow of information and materials while including modules for demand forecasting and production planning.
Due to the real-time visibility created when using ERP, quality management is improved. Problems within the processes can be mitigated quickly due to the responsive supply chain made with ERP technology. Enhanced quality management helps to produce defect-free products.
As a result of ERP capabilities, collaboration is made more accessible, and lead times are reduced. Cost control is even improved because ERP has financial management modules. These modules help identify areas of inefficiency and waste.
WMS
Warehouse management systems (WMS) help support lean supply chain management in several ways. First, it provides real-time visibility into the warehouse operations, which helps prevent overstocking and stockouts, which contributes to lean supply chain practices. Order fulfillment is streamlined between picking, packing, and shipping processes. The WMS has cycle-counting features and helps maintain accurate inventory records. This helps reduce errors and eliminate waste.
Other benefits of utilizing a WMS include optimized space utilization, which helps ensure efficient storage and product retrieval.
Another advantage of using WMS is that it integrates with many technologies like conveyor systems, RFID, and automated guided vehicles (AGVs). These integrations also add to the waste-reduction capabilities of the WMS and support lean goals of waste reduction. WMS generates data and analytics, which helps to refine processes and prompt continuous improvement initiatives.
Both ERP and WMS play crucial roles in supporting the supply chain. Both technologies provide efficient and data-driven operations that help contribute to waste reduction, continuous improvement, and lean methodologies.
Automation & Robotics
Yet another exciting way lean supply chain principles can be optimized is through automation and robotics! Automation and robotics technologies offer many of the same benefits as the technologies previously discussed above. The factors that separate automation and robotics from the rest will make your operation a cut above the rest when incorporating them. For instance, manual errors are significantly reduced. Machines are programmed to perform tasks precisely and do so consistently.
Humans are prone to data entry errors and assembly and quality control errors. Another benefit of automation is that robots do not need breaks and downtime like humans do. Robots can work around the clock, 24/7, boosting production and reducing cycle times. Despite being speedy, these machines have improved quality control over their human counterparts. They can perform high-quality and accurate quality-control checks, reducing the chance of customers receiving defective products.
Robots come in handy big time when it comes to repetitive tasks. Another pitfall of human factory workers is their fatigue, making robots perfect for repetitive and routine tasks. With the help of robots and automation, humans can instead focus their efforts on creative tasks, problem-solving, and complex decision-making. This makes for better resource utilization because machines are used for repetitive, labor-intensive, or dangerous tasks that can be better left to the machines.
Machines can operate continuously, 24/7, making it much easier to meet tight deadlines and accommodate various production schedules. The increased productivity helps to reduce costs due to reduced labor costs, lower error-related expenses, and improved resource allocation/utilization. Lastly, companies implementing automation and robotics have a competitive advantage. These companies operate more efficiently and deliver higher-quality products. Higher efficiency translates to more sales and improved responsiveness to market demands, helping secure their industry leadership.
Automation and robotics can streamline manufacturing processes, allowing companies to easily create leaner, agile, and competitive supply chain operations.
Common Challenges
(Like resistance to change and lack of employee engagement)
As transformative as implementing lean supply chain practices can be, at least in the beginning, resistance can be expected from both employees and stakeholders. Some common challenges include but are not limited to the following:
- Resistance to change
- Lack of employee engagement
- Lack of top-down support
- Lack of standardization
- Inadequate communication
- Short-term focus
- Lack of metrics and measurement
Strategies & Solutions
Resistance to change:
Communicating the benefits and reasons for change to your team is critical. Be sure to emphasize the benefits for individuals and the organization itself. Training and educational sessions can help employees understand the principles and objectives of the lean supply chain. It also helps to have employees involved in the planning and decision-making process and to encourage collaboration and feedback between employees. Lastly, sharing success stories and highlighting the positive impact on other companies and organizations can be very helpful.
Lack of engagement:
Engagement will be higher if employees fully understand the value and buy into lean principles. Providing comprehensive training and fostering a learning culture will likely boost employee engagement. Leadership quality also makes a huge difference. Leaders must actively engage with employees by addressing their concerns and communicating effectively to increase employee engagement.
Lack of top-down support:
Leadership support is essential to implementing lean principles; otherwise, company efforts may need more direction and support. Your company leaders need adequate training on their role and lean supply chain principles. One of the most critical steps is communicating expectations to leaders and their performance goals and metrics.
Lack of standardization:
Standardization is critical to consistent processes and supply chain effectiveness. Make sure to communicate the standardized operating procedures, making sure employees are updated and trained. Visual management comes in handy here. Use visual management tools to create standards, workflows, and performance metrics that are easy to understand. Visual cues can also help to identify deviations from the standards. Monitoring processes and determining areas that can be standardized will also help implement and refine the standards.
Inadequate communication:
Communication is always important within businesses, especially when implementing new standards and procedures. It is vital to establish an open dialogue for feedback and questions, sharing information, and addressing concerns. Ensure that regular updates on the progress of the lean initiatives are provided using various communication channels to keep the team informed and recognize their accomplishments and milestones.
Short-Term Focus:
Companies need to focus on long-term sustainability, not just the short-term gains of implementing a lean approach to the supply chain. Your team can accomplish this by educating on the long-term benefits of lean practices on the competitiveness and sustainability of your organization. Emphasize to your team that becoming “lean” is a journey, not an instant 180.
Align lean initiatives and practices with your organization’s strategic goals and long-term vision. Using balanced metrics considering short-term gains and longer-term strategic objectives will help evaluate success, customer satisfaction, employee engagement, and process efficiency.
Lack of metrics and measurement:
Measuring the effectiveness of the lean supply chain with proper metrics and measurements is essential to determine how the practices and principles impact your supply chain. First, define KPIs (key performance indicators) that align with crucial lean principles and organizational goals. Metrics should be related to efficiency, lead times, quality, and customer satisfaction. Performance Reviews are also essential to identifying areas for improvement and celebrating success! Lastly, creating a culture of data-driven decision-making can boost continuous improvement efforts, engagement, and successful implementation of lean practices.
Risks and Pitfalls
- Overemphasis on cost reduction
- Supplier reliability issues
- Inadequate risk management
- Lack of flexibility
- Poor communication
- Insufficient training and change management
- Inadequate technology integration
- Unrealistic Expectations
- Inadequate supplier collaboration
- Single-Point Failures
Strategies
- Balance cost reduction
- Choose reliable suppliers and develop contingency plans
- Manage Risk
- Incorporate flexibility and agile manufacturing into the supply-chain design
- Clear communication
- Comprehensive Training
- Technology Integration
- Realistic Expectations
- Supplier Collaboration
- Single-Point Failures
- Continuous improvement
Conclusion
Implementing lean-supply chain practices and principles into your supply chain is an excellent way to boost efficiency and reduce waste. Companies that adopt a lean supply often benefit from increased customer satisfaction due to higher product quality, reduced lead times, and lowered costs. Adopting these practices and operating procedures will take time and effort, but the payoff is worth it for companies committed to continuous improvement.
Frequently Asked Questions
Q. What are the 5 principles of lean methodology?
The five core principles of Lean methodology are designed to enhance efficiency in the workplace. They include
- Identifying value from the customer’s perspective.
- Mapping the value stream to analyze and streamline processes.
- Creating a seamless workflow.
- Implementing a pull system to reduce waste.
- Striving for continuous improvement toward perfection.
Q. What is a lean & agile supply chain?
A lean supply chain focuses on efficiency and cost reduction by minimizing waste, while an agile supply chain prioritizes flexibility and speedy response to market changes. Companies can integrate both for a hybrid approach, leveraging lean efficiency with agile adaptability to optimize their supply chain management.
Q. What is lean and Six Sigma in the supply chain?
Lean and Six Sigma in the supply chain refer to strategies for improving efficiency and quality. Lean focuses on minimizing waste to optimize the flow of products, while Six Sigma uses data-driven methods to reduce defects and variability. Together, they enhance supply chain operations by streamlining processes and improving reliability.
Q. Is Apple's supply chain lean?
Yes, Apple’s supply chain is exceptionally lean. They maintain minimal on-site inventory, streamlining their retail spaces and focusing on online orders. This efficiency is boosted by high-tech inventory management systems, ensuring optimal stock levels to meet consumer demands efficiently and cost-effectively.